Exclusives
Environmental Success for CPGs
Grocery Manufacturers Association finds progress, innovation and environmental stewardship among food and beverage product companies.
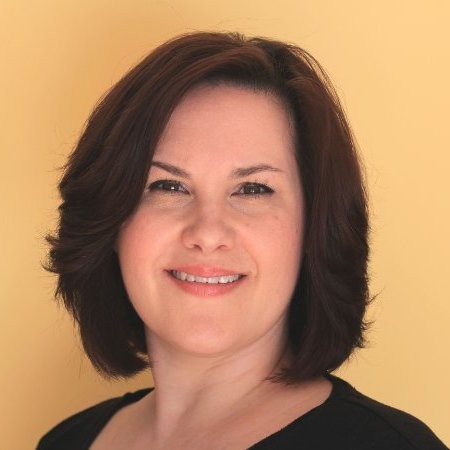
By: Joanna Cosgrove
Just because environmental responsibility seems to be a given nowadays it doesn’t mean that it’s easy being green. Food, beverage and consumer products companies have been working hard to reduce their respective environmental footprints, especially as they relate to air, water and waste management, according to a new report from the Washington, D.C.-based Grocery Manufacturers Association (GMA), which spotlighted some of the industry’s most noteworthy success stories.
“Food, beverage and consumer products companies have a longstanding commitment to improving the lives of consumers, and that includes environmental stewardship,” said Pamela Bailey, GMA president and CEO. “This report showcases not only the considerable progress GMA members are making towards greener facilities, supply chains and products, but also the innovation and creativity that has made this progress possible.”
The range of criteria considered included energy efficiency, carbon reduction, waste reduction and disposal (including reuse and recycling), and water recycling and conservation. Each of the stories selected for the report demonstrated some or all of the following elements: innovation in system or product design; a quantifiable return on investment; engagement or collaboration with external stakeholders; and reduction or improvement in efficiency of environmental factors.
The report highlighted a diverse cross-section of initiatives from an equally diverse slate of manufacturers. The success stories include companies that are converting inedible food waste to energy, reclaiming water from the manufacturing process, and cutting emissions with underground limestone refrigerated storage facilities.
In addition to covering Johnson & Johnson’s use of solar panels, Colgate’s and Procter & Gamble’s packaging redesigns that yielded sizable reductions in the consumption of non-renewable resources, and Cargill and Smithfield’s reclaiming and reuse of meat processing byproducts, the report spotlighted a variety of out-of-the box solutions.
A few companies capitalized on unique opportunities that were right under their proverbial noses the whole time. For Kraft Foods, a prime opportunity wasn’t so much under its nose but underground, beneath its Springfield, MS, plant. Rather than using conventional refrigeration storage facilities the plant made use of underground natural limestone caves situated below the company’s manufacturing plant. According to Kraft, the location took advantage of “natural insulation” and enabled the site to use 65% less energy than it would have with conventional storage. The cave’s central location also saved the company transportation resources, whittling away 1800 metric tons of CO2 emissions, 180,000 gallons of fuel and 1 million miles of truck travel annually.
Nestlé USA’s beverage manufacturing facility in Freehold, NJ, found a unique way to capture energy and avoid waste. Working with a producer of fireplace logs, spent coffee grounds were turned into fire logs—a product that produced significantly fewer emissions than wood. The product also provided the company an additional revenue stream.
Burt’s Bees ratcheted up its commitment to the environment in 2010 by becoming the first zero waste-to-landfill sites in its parent company The Clorox Company’s network. The initiative entailed the reduction, reuse, recycling or composting of at least 90% of the waste streams at the site; the rejection of any commonly recycled items (paper, plastic, corrugate or aluminum) in remaining waste, and the disposal of the remaining 10% of waste to a waste-to-energy facility. The momentum of Burt’s Bees commitment has encouraged other Clorox facilities to follow suit, inspiring a Clorox Tampa, FL, facility to attain zero waste-to-landfill status in 2011. Two additional Clorox facilities are expected to attain this designation at some point this year.
Water is a critical resource in food processing. In fact, the GMA report likened the industry’s ongoing water conservation efforts to similar efforts in carbon reduction. One company that figured out a great way to make the most of its water situation was ConAgra. The company’s fresh-pack facility in Helm, CA, which processes up to 5000 tons of raw tomatoes per day during peak season, reconfigured its tomato paste-making process to capture the water removed from the raw tomatoes. The reclaimed water is used to supply the site’s boilers, cooling towers and tanks, getting re-circulated up to three times before being discharged and reused as agricultural irrigation. ConAgra reported that its “tomato water” helps the company conserve nearly 56 million gallons of water annually, which they said was equivalent to the amount consumed by 560 average-American households in a year.
Ms. Bailey said companies are increasingly driven by the idea that sustainability is a journey, not a destination. “They will continue their drive to find new and innovative ways to reduce their environmental footprint and preserve natural resources while providing consumers with the high-quality products they expect from our industry.”