Features
Packaging & Equipment Essentials
These critical components of doing business can’t be overlooked.
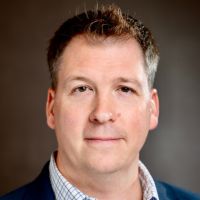
By: Sean Moloughney
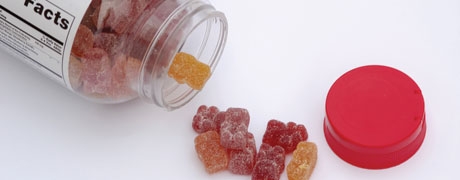
Just as technological innovation has helped improve product formulas and formats, advances in packaging, production, laboratory and inspection equipment are helping companies deliver top quality wellness products.
From a consumer point of view, packaging often presents a product’s first impression. The type of packaging a company will choose often depends on the dosage form (e.g., powder, tablet, liquid, gummy, etc.), noted Marny Bielefeldt, director of marketing, Alpha Packaging, Bethpage, NY, which manufactures plastic bottles and jars ranging in size from one ounce to two gallons for solid and gummy forms of vitamins and minerals, liquid energy shots, powdered protein products and other dietary supplements.
Picking the Right Package
Ms. Bielefeldt offered some perspective on issues to consider when companies are choosing the packaging type that fits their product best.
“How will it be dispensed, and has a specific closure been selected? Does the bottle need to be squeezable, or should it be rigid? All of these affect the selection of the packaging material, and that is why most of our stock lines for the supplement industry are available in both polyethylene terephthalate (PET) and high density polyethylene (HDPE).”
Ms. Bielefeldt said Alpha Packaging has seen a dramatic increase in the number of dietary supplements in gummy format, as opposed to traditional tablet or capsule forms.
“The gummy trend has created a need for wider-mouth, straight-sided packaging, since gummies are both larger than most traditional supplements and also stickier. The wider mouth allows the consumer to get his or her fingers into the container to pick out individual vitamins, and the straighter sides also make it easier to pour gummies out of the container. Most of the gummy packaging that we make at Alpha Packaging is clear PET, because the gummy vitamins are usually brightly colored, and the brand owners want people to see the product inside the package.”
However, if the contents of the bottle are unattractive, companies may want an opaque PET or HDPE bottle, she added. “Also, if you have a powdered supplement that settles a lot after it is filled, you want something opaque or fully-labeled to disguise the fact that the bottle looks partially filled by the time it reaches the consumer.”
Container manufacturers also need to help companies comply with certain environmental standards such as California’s Extended Producer Responsibility laws, Ms. Bielefeldt noted.
“We are getting a lot of requests to ‘light-weight’ our bottles by 10% or more, and there is a fine line that you have to manage when light-weighting rigid packaging for the nutritional supplement industry, since the bottles must be able to be filled and labeled at very high speeds, and be strong enough to withstand stacking during shipping and at retail. We feel product protection is one of the most important roles of rigid plastic bottles, so we are careful not to take too much plastic out of the protective bottle.”
Overall, nutraceuticals can be processed and packed in many different ways depending on the specific application and the product nature, noted Charles Ravalli, CEO of Romaco, Lincoln Park, NJ, which offers tableting and packaging solutions for pharmaceutical, food, cosmetics and healthcare markets worldwide. The company’s product portfolio includes primary and secondary packaging, aseptic liquid/powder filling and tablet press technologies.
“Brand images are often conveyed by stylish packaging,” said Mr. Ravalli. “Manufacturers should keep in mind that eye-catching packaging design should be realized cost efficiently to achieve the desired effect. This requires state-of-the-art packaging equipment that provides operational effectiveness and quality.”
Integrated solutions from Romaco for tableting and packaging can be configured individually according to customer needs, and Romaco offers a mix of standard modules and customized features, according to Mr. Ravalli.
For example, the Romaco Kilian equipment range is suited for the production of single and multilayer tablets in different sizes and shapes, effervescent tablets and beads. When it comes to the packaging of nutraceutical solids, Romaco offers single dose solutions for blister packaging (Noack) or strip packaging (Siebler), depending on the characteristics of the tablets.
Effervescent tablets are extremely sensitive to light and moisture and need to be packed into four-side sealed foil packs, which can be produced on Siebler strip packaging machines, Mr. Ravalli said. “In this case the tablet press can be directly connected to a heat-sealing machine in order to prevent the fragile effervescent tablets from breaking. After tableting and primary packaging has occurred the nutraceutical product can be packed into cartons and shipping cases.”
In terms of technological advances in the equipment and packaging field, Mr. Ravalli noted the general automation level of packaging processes has been increasing greatly in recent years. “The implementation of servo drives and robotic systems ensure high precision and provide more flexibility.”
With its Siebler FlexTrans Series, Romaco offers high flexibility when four-side sealed foil strips are conveyed to a cartoner for secondary packaging. Up to six FlexPicker robots pick and place up to 900 strip packs per minute, according to the company.
Robots handle different pack sizes, layouts and stack heights and work almost completely independently of specific format parts.
“This results in excellent overall equipment effectiveness (OEE) values even when it comes to product and format parts changeovers, which result from small to medium batch sizes. OEE is defined by quality, performance and availability and remains the main challenge for modern packaging processes.”
Nutraceutical manufacturers should evaluate the whole process and condition of their packaging concept, Mr. Ravalli suggested. “An integrated solution should provide high product quality and high production efficiency. Machine interfaces shouldn’t cause obstacles. Furthermore, manufacturers should analyze their frequency of product and format changeovers and define the level of flexibility they need to produce their average batch sizes. Cleaning processes and product changes should be optimized continuously. This also applies to ergonomic features, general compliance and user-friendliness of the equipment.”
Nosco, Gurnee, IL, offers printed packaging from structural/creative design to completion, including printing of labels (digital and conventional), cartons (digital and conventional), multi-panel labels, package inserts and blister lidding. The company also offers support services in material selection, structural design, graphic design, specification development and packaging line engineering support.
Ultimately, packaging serves two primary functions in the nutraceutical industry, according to Brent Anderson, packaging advisor at Nosco. The first is to protect the product and ensure consumer safety. “This includes materials engineered to support the integrity of the product through manufacturing, environmental changes and end use,” he noted. “The second function of packaging is to serve as a sales and promotional canvas for the brand. As the nutraceutical industry continues to grow, it becomes increasingly difficult for brands to stand out from the competition. Nosco understands the importance of differentiation and has expertise in decorative features including unique substrates, metallics, soft touch/high gloss coatings, embossing and foil stamping.”
Technology has rapidly progressed in printed packaging over the last 10 years, Mr. Anderson said. “The single largest advancement in technology has been the shift from conventional print production methods to digital print. Digital print eliminates the use of printing plates, requires less make-ready, and offers unit cost savings on short-medium run packaging.”
Nosco recently became the first printer in the U.S. to produce digital sheetfed cartons on the HP Indigo 30000, he added. “This technology impacts the nutraceutical industry by providing shorter lead times (5-10 days), eliminating costly plate charges and allowing for the incorporation of variable data. As an example, Nosco was involved in printing digital labels for the ‘Share A Coke’ summer campaign which drove sales growth for Coke.”
Companies should consider packaging that will increase manufacturing speed, enhance the brand image, improve functionality and convenience for the consumer and drive sales, Mr. Anderson said.
Well Equipped
As the market for healthy food, beverage and supplement products continues to grow, and regulatory matters come into focus, quality control/assurance will be critical to a business’ long-term success.
Like any up-front, large capital expenditure, companies want to be sure they will be getting a good return on their investment. “Sophisticated, high-speed, efficient inspection equipment can be deemed costly when viewed as a capital cost,” said Robert Rogers, senior advisor for food safety and regulation, Mettler Toledo Product Inspection. “However, these are well-built machines that perform continuously and tirelessly for years, often freeing labor for other projects within a facility. Viewed in terms of their long-term assurance of quality, product safety and protection against recalls and even liability lawsuits, they are a valuable investment that provides an almost immediate measurable return.”
The Mettler Toledo Product Inspection Group, consisting of CI-Vision, Hi-Speed and Safeline, supplies in-line checkweighers, machine vision systems, metal detectors and X-ray inspection systems. Mettler Toledo’s ProdX collects and stores data from these inspection systems. “Many industries, including nutraceuticals, use these solutions to ensure the quality and safety of their products and improve the efficiency of their manufacturing and packaging processes,” said Mr. Rogers.
Specific inspection systems can review various supplement formats—liquid, powder, capsule, tablets, etc.—efficiently and thoroughly, “at speeds that do not slow production, and remove non-compliant products before they can leave a facility and enter the marketplace,” Mr. Rogers added.
Advanced systems not only help companies improve their productivity and product quality, but new technologies that collect, store and retrieve inspection data are also typically the first thing FDA will request in the event of an inspection visit, he noted.
Signed into law in January of 2011, the Food Safety Modernization Act (FSMA) represents a major shift in the regulatory landscape, according to Mr. Rogers. “Previous laws have identified dietary supplements as food, and the likelihood is that supplements will soon be covered by FSMA as well,” he speculated. “Many manufacturers and processors of nutraceuticals and supplements are rigorously informing themselves now as to how FSMA will affect their businesses, and are preparing to comply.”
He continued, “One of the critical assets that food companies have used to comply with FSMA requirements, and that will serve the nutraceuticals industry as well, is systematic, machine-based inspection of products and packages to detect and reject contaminated or otherwise non-compliant products or packaging, while maintaining accurate, complete records of those actions.”
In addition to confirming that the inspection equipment they are evaluating for purchase will provide the capability and speed they require, companies should also evaluate the company behind the equipment and the support services it offers. Available training, technical support and timely repair and parts delivery are an essential part of ensuring that the equipment continues to operate effectively and with minimal downtime, Mr. Rogers suggested.
Weights & Measures
Brookfield Engineering Laboratories, Middleboro, MA, specializes in test instruments for measuring flow properties of liquids, semi-solids and powders. Viscosity measurement, texture analysis and powder flow testing are Brookfield’s three major applications. Inks, adhesives and sealants are examples of packaging materials that are tested using Brookfield Viscometers while the Brookfield Powder Flow Tester analyzes flow behavior.
R&D personnel evaluate new formulations with Brookfield Viscometers, Texture Analyzers and Powder Flow Testers, according to the company. Benchmark values for acceptable flow behavior are established and given to the quality control department, which then uses the same instruments to make measurements on production batches and verify acceptability, explained Bob McGregor, general manager, Global Marketing, Brookfield Engineering.
Overall, lab instruments have become “smarter,” he added, and “when programmed according to the test procedure defined by R&D, can give automatic pass/fail determinations on production batches of material. In line process viscometers can potentially identify out of spec material before the fill stage where product is put into its shipping container.”
When evaluating which packaging and/or equipment to use, companies should talk with other companies that produce established name brands and find out how they test for viscosity, texture and powder flow behavior, he suggested. “The best reference is a company whose product enjoys strong market recognition for consistency and quality.”
Production Needs
Fette Compacting America, Rockaway, NJ, manufactures high-speed rotary tablet presses for use by nutraceutical, pharmaceutical, confectionery and other industries. “Our presses are renowned for their unique blend of ultra-high precision and tank-like robustness,” said Matt Bundenthal, director of sales & communications manager. “We actively work with and support many leading manufacturers of nutraceutical and vitamin-based products.”
High-speed rotary presses play an integral role in the equipment line-up of any nutraceutical manufacturer producing goods in tablet form. Fette was one of the first companies to develop and perfect the rotary tablet press, according to Mr. Bundenthal. “Once the domain of lower-cost machines, nutraceutical companies in recent years have moved toward standards approaching those of pharmaceutical companies, and their equipment acquisitions have followed suit. They recognize the overall value offered by companies like Fette Compacting, in the form of presses that run faster, more reliably and with less product loss.”
Higher-tech presses such as those offered by Fette Compacting result not only in greater reliability, but also greater repeatability, he added. “It is easier for manufacturers to replicate good results with such equipment. They are also easier to integrate with upstream and downstream equipment such as packaging lines and/or conveyance mechanisms, making them more appropriate for continuous manufacturing trains.”
Fette offers complete services to clients in the U.S., Canada, and Puerto Rico, including new and used machine sales, technical assistance and installations. Other products and services include training classes and seminars, laboratory trials, validation, maintenance, trouble-shooting and repairs, spare parts and tooling.
Other factors companies should consider when evaluating equipment, according to Mr. Bundenthal, include ease of changeover and maintenance; the ability to maintain precise weights, thickness and hardness at target and high speeds; technical capabilities for integration with other equipment; and the vendor’s local support network, ability to dispatch technicians and spare parts inventory.
Pharma Technology Inc. (PTI), Fairfield, NJ, designs and manufactures specialty tablet dedusters and capsule polishers along with metal detecting devices and loading systems for tablet- and capsule-producing machinery. Since its founding in the greater Brussels, Belgium area in 1991, PTI has been developing complete handling solutions for tablets and capsules tailored to specific niche requirements.
“PTI’s patented concurrent flow dedusters efficiently remove dust on tablets and check for any metal contamination directly after compression,” said Nic Michel, general manager. “This helps prevent downtime on packaging equipment downstream and ensures a quality product is packaged. Capsule polishers also remove empty, broken or half capsules.”
A differentiator common to PTI equipment is vertical height gain, made possible by the company’s innovative machine design, he added. “The taller the outlet height, the larger an output container can be used, which in turn yields the possibility of needing only one operator rather than two—even when running a double-sided tablet press or a high-speed capsule filler.”
Elevating dedusters and capsule polishers move tablets/capsules upward vertically during process to allow improved handling into taller containers or continuous processing, Mr. Michel said. In both cases, this allows for a more streamlined process with less floor space requirement and less frequent interruptions during manufacturing and packaging of product batches. Integrated tablet testers also help ensure consistent, high-quality products, thus reducing the number of lost batches and allowing segregation of bad tablets during a batch.
In addition to providing ancillary and connectivity equipment for a variety of tablet presses and capsule filling machinery, PTI also serves as the exclusive North American distributor of Roeltgen Marking Systems’ state-of-the-art FLEXITAB line of tablet presses. Any machine, equipment or service provided by PTI in North America comes with available engineering and maintenance services to ensure successful factory integration and continued product performance.
Uhlmann Packaging Systems, Towaco, NJ, offers blister- and bottle-machines, cartoning systems, line-monitoring and control systems, and downstream packaging machinery for the North American pharmaceutical and nutraceuticals industries, along with sales support, service technicians, on-site training, parts inventory, tool manufacturing and rebuilt machinery, and on-site engineering for line integrations.
“We provide complete packaging lines (filling to palletizing) in blisters or bottles that include tablets, capsules, caplets, soft gels, etc.,” said Ralf Klotz, regional sales manager. “Uhlmann’s equipment and engineering technology has increased line speeds, efficiency, flexibility and productivity with its customers. This has allowed companies to package more products while reducing labor, which of course leads to higher levels of cost-effectiveness and profits.”
Along with the equipment and packaging materials themselves, companies looking for equipment partners should consider a supplier’s post-sales service capabilities, including spare parts, tooling, training, etc., Mr. Klotz suggested.
MG America, the U.S. subsidiary of MG2 of Bologna, Italy, a supplier of processing and packaging equipment, offers the MG2 SELEKTA, a high-speed checkweigher and sorting machine for the production of tablets. SELEKTA delivers exemplary accuracy at high speeds, and offers wide flexibility in terms of the product shapes and sizes it can handle, according to the company.
Depending on the product, SELEKTA can check up to 500,000 units per hour. This innovative technology is designed for seamless integration with existing tableting equipment, which allows for continuous process manufacturing.
Omega Design Corporation, Exton, PA, a global provider of innovative packaging machinery and serialization solutions, recently partnered with Brazil-based packaging equipment provider Grupo Tecnor to introduce a jointly-developed semi-automatic case packer with unit-level serialization capabilities to the North American market. The ECX-001 Case Packer has been outfitted with special software, cameras and printers from Omega Design to meet more stringent track and trace requirements mandated by the Drug Quality and Security Act, which became U.S. law in November 2013.
By offering semi-automatic functionality, the ECX-001 Case Packer occupies a desirable middle-ground in both case packing and serialization, the company said. The machine stands as a simple, economical way to both increase production and eliminate hand packing costs while avoiding the expensive, often time-consuming transition to fully automatic operations.