Features
Pharma/Biopharma Manufacturing & Packaging Equipment Trends
Regulations require quality, products demand flexibility, and clients need equipment be be fast and easy to use.
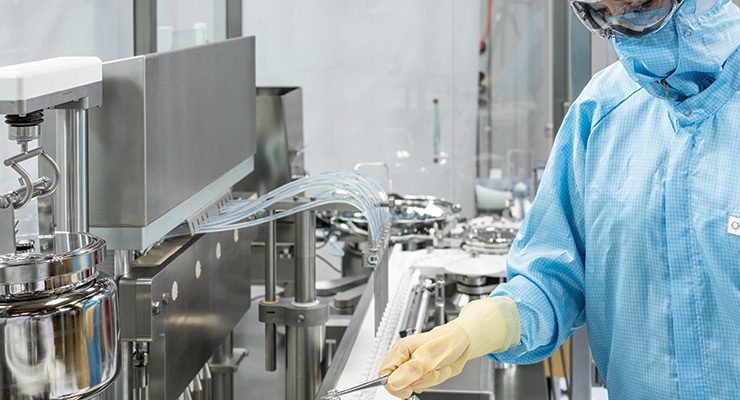
Valued at $65.5 billion in 2015, the pharmaceutical packaging market is projected to reach $94.9 billion by 2021, with an annual growth rate of 6.4% from 2016 to 2021, according to MarketsandMarkets Research. As pharma/biopharma drug products evolve, and with serialization regulatory mandates upon us, packaging needs are growing and changing rapidly.
Packaging equipment must address the specific challenges new drug products present. Pharmaceuticals require reliable packaging solutions that provide product protection, patient ease and security, information and identification of products.
While tablets or capsules still account for most medicines, other delivery methods are increasingly being used, such as prefilled syringes, inhalation, and transdermal. Additionally, developments for anti-counterfeit measures and compliance packaging add complexity, resulting in the need for more tailored packaging solutions.
Equally significant, the FDA approved a record number of personalized medicines in 2017, which now account for more than one in four New Drug Approvals. This growth of personalized medicines and the need for smaller batches has resulted in filling lines that are smaller, more modular, flexible, and with shorter lead times.
This article will discuss some of the key trends shaping pharmaceutical packaging and equipment and the capabilities needed for today’s pharma/biopharma products.
Pharma & Biopharma Trends
The sustaining trends impacting equipment needs are new, specialized, and highly potent drug products along with smaller volumes, as well as continued serialization efforts—all of which require flexibility. “There have been groundbreaking developments in pharma and biopharma research, for instance for the treatment of cancer and autoimmune diseases. These call for especially flexible filling and packaging equipment that can be adapted to new products, as well as different packaging formats, quickly, with short changeover times,” said Christian Treitel, director strategy and business development, Robert Bosch Packaging Technology GmbH.
Also, safety concerns during the drug production process have led to the growth in containment solutions and barrier technologies. “Compared to a couple of years ago, the number of new production lines equipped with isolator technology has risen from three to five out of 10 today. This demand will continue to grow in accordance with the highly potent drugs that will be released to the market in the coming years,” Mr. Treitel added.
Highly specialized products require equally complex operations and equipment. Tim Saarinen, chief operating officer of Medical Packaging Machinery for Maruho Hatsujyo Innovations, said, “Active ingredients continue to become more complex and specialized. These products typically require higher barrier from moisture and oxygen than traditional products in addition to sometimes requiring specialized delivery systems. Overall, the trend is for more customization to meet the specialized packaging needs of new specialized drugs and their delivery systems.” According to Mr. Saarinen, there is a perpetual effort to reduce healthcare costs, which is driving equipment manufacturers to provide faster and more economical equipment of the highest quality.
Another trend is the greater variety of types and ways to administer the drugs. According to Matthias Poslovski, technical sales director at OPTIMA pharma GmbH, “The self-administration of drugs or safety devices may require special assembly functions within the packaging process. Other APIs can be delivered by oral dispersible films (ODF). The processing of these pharmaceuticals is achieved by combining converting and packaging technologies.”
While serialization has been a long time coming, it remains an important aspect for equipment and the software solutions that go with it. According to Mr. Treitel of Bosch, “The aim should be to establish a holistic serialization solution that is in line with the different national or regional guidelines and laws, and which follows a multi-level approach from labeling and attributing serial numbers through to managing and storing them across the company IT and in relevant databases.”
Additionally, the packaging market is being influenced by changing consumer habits that are impacting the retail marketplace, namely the rise of e-commerce. According to Vladimir Spehar, director, strategic business development at Jones Contract Packaging Services, “There has been a $4.3 billion market shift to online, dollar store and warehouse club store channels. As a result, our brand partners are beginning to offer an increased number of over-the-counter medications within dollar store or warehouse club settings to maintain or gain market share. Jones continues to see an increased demand for packaging and packaging services that meet the needs of these types of retailers, including multi-product blister card packaging for warehouse clubs, and pouch, blister, and purse-pack vial convenience packaging for dollar stores.
He added, “Not only are we seeing higher volumes of convenience packaging with the rise of dollar store retail, but this is also a response to an increasing volume of consumers adopting an “on-the-go” lifestyle. Consumers need smaller packaging for easy storage and this packaging must also be designed with durability and usability in mind.”
Addressing Challenges
Costs and regulatory constraints are inherent in the pharmaceutical industry. Regulatory requirements demand quality, diverse drug products demand flexibility, and clients necessitate that equipment be fast and easy to use in an effort to reduce costs. According to Mr. Saarinen of Maruho Hatsujyo Innovations, “Modern packaging equipment needs to meet a number of challenges simultaneously. The equipment needs to be efficient in terms of throughput and provide the highest quality product. At the same time, it needs to be flexible with rapid and easy change-overs. In addition, packaging a multitude of unique drug products/delivery systems requires more specialized equipment to meet multiple applications.”
“Time and cost pressure combined with very high quality requirements are certainly the most important challenges,” said Mr. Treitel of Bosch. “For us, as equipment suppliers, the challenge is to provide the appropriate equipment and services to enable our customers to achieve a fast time-to-market with highly flexible platforms.”
Another major challenge, according to Mr. Treitel is the growing need for automation and digitization, and aligning it with the strict regulatory requirements of the pharmaceutical industry, for instance regarding electronic batch records and signatures, as well as process validation. To help address these needs, Mr. Treitel said, “Software modules help to control and monitor production and quality data, as well as logistic processes flexibly according to customer requirements. Easy-to-handle user interfaces facilitate the operator’s work, while apps ensure that a transparent overview of machine data is delivered to mobile devices—no matter where the operator or line manager is within the production facility.”
With regard to small batch sizes and aseptic liquids, many customers ask for very flexible capabilities in the machinery, according to Mr. Poslovski of OPTIMA. “The machinery should be able to process vials, prefilled syringes, and cartridges, and the duration for format changes has to be as short as possible. Or even better, there is no need for format changes at all; by implementing new transport systems or robotics, this is achieved for almost all format sizes, and even container types. High flexibility means less down time. If isolator technology or freeze-drying is necessary, which is the case within many projects, the decontamination cycle or the duration of the freeze-drying process has to be addressed,” said Mr. Poslovski.
As a packaging supplier, equipment must be able to handle a variety of products and circumstances with speed and agility, while meeting requirements. Mr. Spehar of Jones Contract Packaging Services, said, “More than ever, our customers are faced with market challenges that require them to respond quickly with new product launches, modifications to existing products, and more. This means we need to be nimble and responsive so our customers can ensure their products enter the marketplace as quickly as possible, while complying with all the necessary regulatory and quality standards. With this in mind, we typically seek unit-dose, high-speed equipment with a quick changeover to accommodate timely, short run jobs when evaluating new equipment investments.” Mr. Spehar added, “It’s also important our equipment and capabilities respond to regulatory requirements. For example, our packaging lines must accommodate new packaging designs compliant with the Health Canada’s Plain Language Labelling (PLL) Regulations.”
Contract packagers serve a varied customer base that includes clients with different needs and requirements. “We need to have equipment that is flexible and can handle a wide range of materials and sizes,” said Joe Luke, vice president of sales and marketing for Reed-Lane. “These include, for example, bottle lines that can handle small to large bottles, squares or rounds, desiccants, topserts or sideserts, and are integrated with serialization including the ability to aggregate. Also, there are more and more products requiring cold storage, which requires the packager to have cold storage capabilities.”
Advances in Packaging Equipment
From liquids and powders to solid dosage, technology to handle these platforms continues to advance. Mr. Treitel of Bosch said, “Continuous manufacturing is one of the most widely discussed topics in the production of oral solid dosage forms at the moment. Apart from the existing solutions, new ones are currently being developed. For example, the new Xelum platform from Bosch combines dosing, mixing, granulating, and tableting in a continuous process, and is based on the tested granulation technology developed by Bosch’s subsidiary Hüttlin.”
In terms of liquid-filling operations, new platforms are able to process different types of containers, like the ALF 5000 from Bosch. Mr. Treitel noted, “Pharmaceutical manufacturers can opt for one out of three versions: ampoules, vials, or both container types on one machine. At the same time, high accuracy in filling volumes is extremely important, especially for manufacturers of cost-intensive medicines such as cytostatics. Consequently, the new vial-only version now includes 100% in-process control, which implies weighing the containers before and after filling to achieve exact filling volumes.”
As far as powder filling is concerned, customers are looking for high flexibility, a compact footprint, and high speeds, according to Mr. Treitel. During a machine presentation in Crailsheim, Bosch launched the new AFG 5000 filling and closing machine with a new transport system, an individually selectable number of filling points and increased output in the high-performance segment.
Mr. Saarineno of Maruho Hatsujyo Innovations highlighted some of the company’s latest advances. MHI’s parent, Maruho Hatsujyo Kogyo (MHK), recently installed blister packaging equipment for highly active pharmaceutical/biologic products where the API is self-contained by the blister packaging machine by combining isolator technology with blister packaging. According to Mr. Saarineno, this reduced the facility’s costs dramatically. He added, “Other innovative solutions offered by MHK include an auto splicer for blister machines along with CapsAlign, a capsule feeder that orients all multi-colored capsules in the same direction.”
Advances at OPTIMA include the 100% bubble-free filling and closing of cartridges. According to Mr. Poslovski, “This is an important precondition for the correct dosing when auto injectors are in use or for processing oxygen sensitive products. Furthermore, we have launched our MultiUse Filler systems that offer the most flexible, automated and safe processing of small to mid-sized batches. Our sister company, Metall+Plastic, has developed a new technology for further reducing decontamination cycles, called Decojet. Also, at Achema, the freeze-drying division at Optima Pharma, will present a new process for controlled nucleation. It leads to better quality of the freeze-dried product and the potential for new time savings.”
There are numerous variables influencing packaging today. Not only are the drug products and delivery methods changing, often becoming more complex, regulatory requirements, personalized packaging, and compliance trends demand more advanced equipment solutions.
Packaging equipment needs to address many of these variables, often in one fell swoop, providing efficiency and quality, while offering flexibility to accommodate a multitude of products. In response, suppliers have streamlined equipment designs to save space, increase speed and flexibility, and added technology and software solutions to keep up with complexities.