Features
Pharmaceutical Equipment Solutions Showcase
Roundup of new and innovative production machinery.
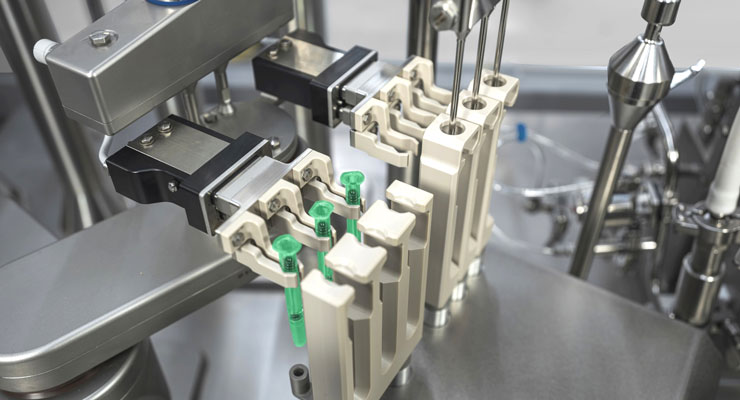
Syntegon Introduces Solutions for Lab-Scale and Small Batch Filling
Syntegon (formerly Bosch Packaging Technology) launched new solutions for lab-scale and small batch filling of solid and liquid pharmaceuticals: the new GKF 60 capsule filling machine and the Versynta Flexible Filling Platform (FFP).
“The need for smaller quantities of highly potent drugs is rising continuously. We have put these solutions in the focus of our current development activities and are proud to offer our customers a number of exciting new technologies,” said Thomas Mauritzen, general manager at Syntegon Minneapolis.
The new GKF 60 capsule filling machine enables the development of new formulations with a wide variety of dosing systems at different OEB levels and with an optional 100% gravimetric weighing system. The mobile machine with only six stations requires little space and few format parts. Familiar dosing modules for DPI, pellets, tablets, or liquids, as well as the mini-bowl station for scale-up to the next larger production machine offer flexibility. Also, the newly developed piezo dosing station makes it possible to accurately fill very small quantities starting at 0.1 milligram filling weight. Customers can choose between a standard, a containment, and a combi solution. The latter can be adapted for both simple and highly potent formulations up to OEB5 high-containment.
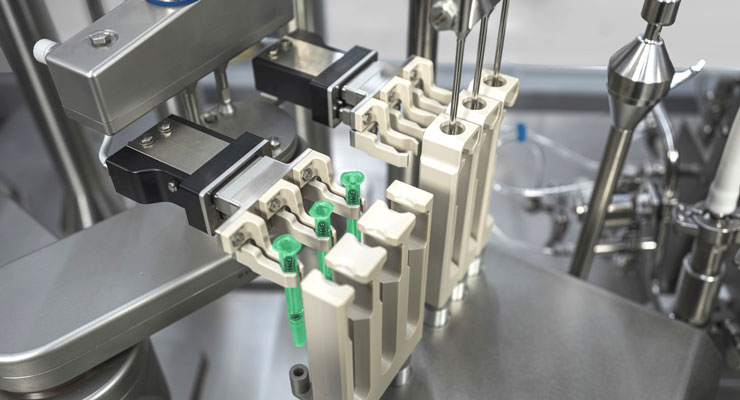
Syntegon’s Versynta FFP was developed for highly potent pharmaceuticals. The modular and individually configurable small batch solution for liquid pharmaceuticals with an integrated isolator is designed to achieve precise product yields at low output. The platform is based on pre-developed and tested modules that can be flexibly combined. It handles different container types such as vials, syringes, and cartridges, and can be converted to different filling systems including single-use solutions. The Pharma Handling Unit, a four-axis robot, allows for safe and gentle transport without glass-to-glass contact. Versynta FFP processes up to 3,600 containers per hour and comes with 100% in-process control.
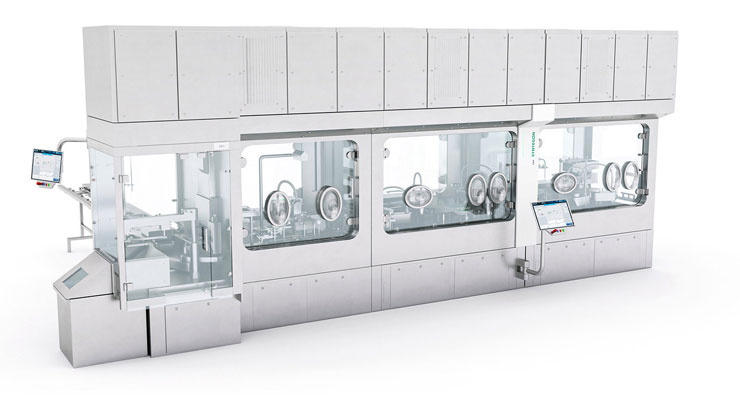
The portfolio is completed by a comprehensive consulting and service offering along the entire machine lifecycle. Syntegon’s customized offerings range from spare parts and field service to stock optimization, modernization, and preventive maintenance, as well as remote and data-based services. All Syntegon machines will be delivered “IoT ready” and provide interfaces for numerous digital solutions.
Steriline Showcases New Robotic Nest Filling Machine
Steriline, an Italian aseptic processing manufacturer, introduced its new Robotic Nest Filling Machine (originally intended for syringe-filling only). The new machine works with the RayDyLyo solution, the all-in-one closure system developed by ARaymondLife which integrates a plastic push-fit cap as an innovative alternative to aluminum caps, and the SG EZ-fill vials in nest by Stevanato Group.
The features of the RayDyLyo closure system are designed to be more suitable to produce small and medium volumes in R&D labs or pilot lines, and Steriline chose to develop a solution working with RTU (ready-to-use) containers. Customers generally request flexible and high-speed equipment for R&D processes, and this solution features a simple and fast changeover that could be executed in a reasonable timeframe, according to the company.
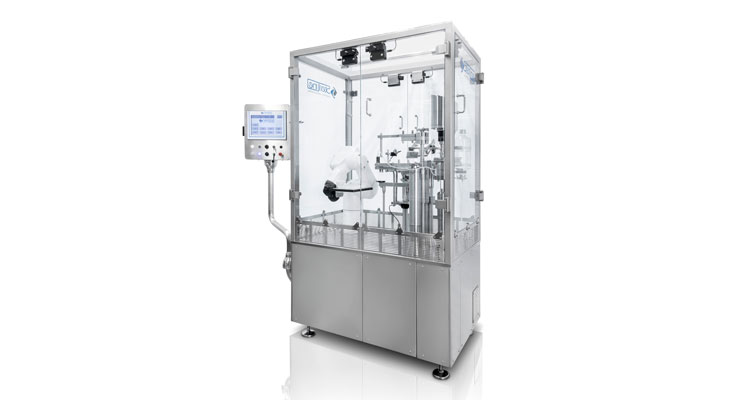
“The development of the machine itself was not too complex since our stoppering and capping system could be very easily adapted to the RayDyLyo system,” said Giovanni Panzeri, area sales manager MEA at Steriline. “Of course, the cap feeding system and stopper/cap pick-and-place unit must be adjusted to the physical characteristics (such as dimensions and weight) of the new caps, which means this must be considered in the design of the equipment.”
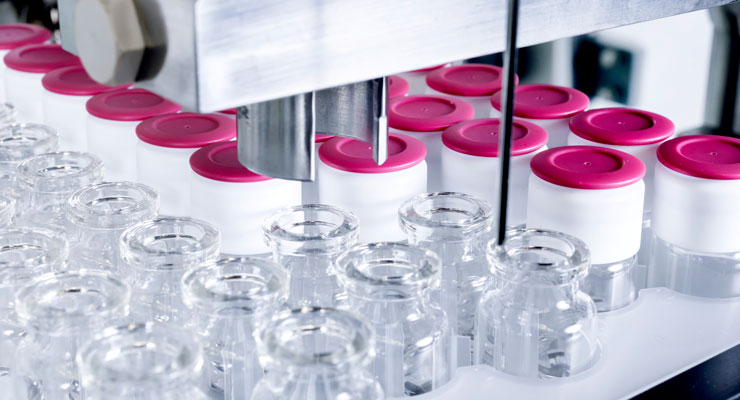
“The pre-sterilized SG EZ-fill vials provide a superior level of quality, compliance, and patient safety,” said Fabio Bertacchini, product management director at Stevanato Group. “Available in Nest & Tub or tray configuration to accommodate different customers’ needs, they are an ideal solution both for clinical batches and commercial production. SG-EZ fill vials seek to maximize filling efficiency, preserve the glass mechanical resistance and reduce particle generation, streamlining production operations.”
Optima Life Science and Optima Automation Showcase New Solutions
Optima Automation, a subsidiary of the Optima Group, showcased a new assembly solution for glass syringes. The OPTIMA GSM has been optimized for even gentler product handling, higher efficiency, and greater flexibility.
The assembly machine covers the processes of tray handling, product separation, inserting, and bonding the cannula as well as various hardness and test procedures.
This solution is optimal for limited space in the clean room. Despite the large number of process steps, the machine footprint is reduced to a minimum by the rotary transfer platform.
According to the company, maximum safety is guaranteed with 100% in-process controls: tension test, flow test, optical inspection of several factors such as the needle’s angular tilt position or checking of bonding surface.
Defective parts are discarded separately to ensure high output. Plastic grippers from the 3D printer allow gentle handling of fragile glass barrels. Also, individual requirements, for example in adhesives, can be considered at any time.
Shawpak Introduces Four-Side Seal Pouch Machine
Shawpak, a U.K.-based medical packaging equipment specialist, has introduced a 4-Side Seal (4SS) Pouch Machine designed for packaging flat medical products. The new Shawpak 4SS can be particularly useful to manufacture pre-made pouches for manual packaging lines.
The 4-side pouch machine is the latest in the company’s portfolio of pouching and thermoforming equipment solutions. According to the company, it was designed with an understanding of brand owner requirements, as well as the limitations in the market’s current standard machinery.
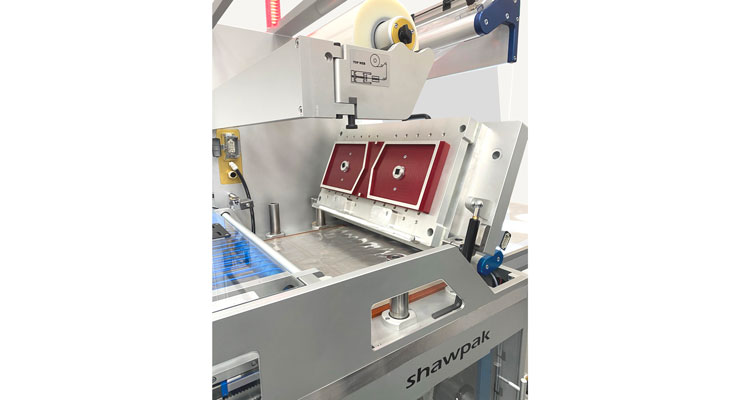
The Shawpak 4SS is designed to:
- Pack flat products to a maximum thickness of 5 mm in packs up to 600 mm x 340 mm;
- Produce up to 4,000 packs per hour;
- Make 3-side sealed pouches with the remaining side open, allowing medical device customers to produce pre-made packs that are manually filled and sealed;
- Incorporate the latest technologies and innovative functionalities; and
- Ensure high efficiency and minimal maintenance.
Thermo Fisher Launches Gibco AAV Production System
Thermo Fisher Scientific has launched the integrated Gibco AAV-MAX Helper Free AAV Production System, a complete, optimized solution that aims to simplify the AAV vector production workflow. The all-in-one AAV-MAX system is designed to increase productivity and cost efficiency by delivering high viral titers using Viral Production Cells 2.0, a new, clonally documented, 293F-derived mammalian cell line.
AAV is crucial to the field of gene therapy; more than 1,300 unique gene therapy products are currently under development, and nearly half are reliant on AAV. The ability to scale production is critical to bringing down costs and accelerating the process from research to commercialization.
“AAV has an efficacy and safety profile that makes it an ideal therapeutic vector and one of the go-to biological delivery methods for the latest gene therapy breakthroughs,” said Amy Butler, president, biosciences, Thermo Fisher Scientific. “The new AAV production system is part of our end-to-end workflow solutions designed to meet growing demand for cost-effective, scalable viral vector production. Having access to products and services designed specifically for cell and gene therapy research, with line of sight to clinical manufacturing, empowers our biotech and biopharmaceutical partners.”
The AAV-MAX system was developed to scale from shake flasks to bioreactors. Coupled with the active development of regulatory-compliant reagents, the system is designed to streamline the transition from research to commercial manufacturing. According to the company, on average, the system can save viral vector researchers and developers 25% on plasmid DNA usage and 50% on production costs compared to polyethyleneimine (PEI)-based mammalian production systems.