Supplier Insights
Blister Packs Improve Gummy Supplement Manufacturing and Product Performance
Along with security, compliance, shelf life and product integrity, blister packaging may also simplify gummy processing methods.
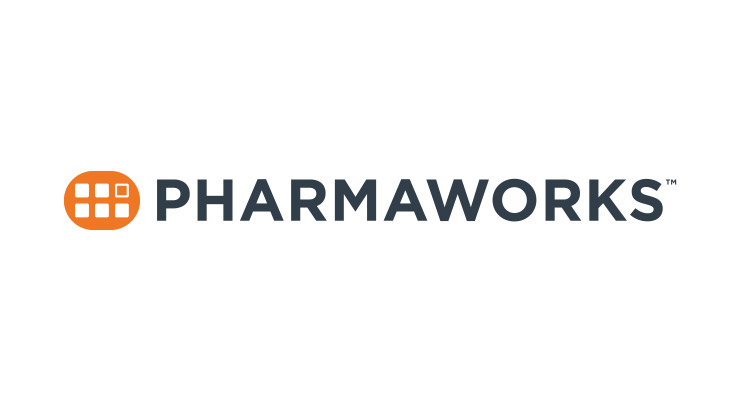
Released By Pharmaworks LLC

Nutraceuticals World (NW): Has Pharmaworks seen any increased interest in gummy packaging in blisters?
Ben Brower, Vice President and General Manager, Pharmaworks LLC: There definitely has been an increase in activity. Both customers and other OEMs have been contacting Pharmaworks to find out how our line of blister machinery can play a role in new packaging concepts. Both customers and other OEMs report manufacturing capacity to be nearly sold out for the rolling 12-month period starting Q4 of 2022.
NW: Why is the blister package a good method for packaging gummies?
Brower: Blister package offers several advantages as a packaging method. By nature, the blister package is a unit of dose type package. Typically, there is one piece of product per blister cavity and subsequently several blister cavities on a blister card. Therefore, the consumer or patient can take one product without disturbing the integrity of the other products on the blister card. This is significant for several reasons.
Labeling: Each cavity can be labeled with Lot and Date coding, product name and strength, and can have barcoding. This ensures an individual knows what they are consuming.
Security & Compliance: Each individual cavity/unit of dose ensures the product has not been compromised. Additionally, patient compliance is typically better as the patient or consumer knows how many products have been consumed. Some blister formats have sequential labeling to remind the patient on what day to take the product.
Shelf Life/EXP: Since each piece of product is sealed in an individual cavity, product integrity and shelf life are consistent and longer than other forms of packaging—especially if the product is moisture and/or light sensitive. Blisters can be cold-formed, which is the highest level of light- and moisture-protection available.

NW: Are gummies being looked at for medication delivery as opposed to supplement delivery?
Brower: As most consumers know, the gummy technology is widely used for nutraceutical products and can be formed into many shapes and sizes. Gummies by design are meant to be chewed rather than swallowed, making the product a good delivery method for older patients and children. Recently, Pharmaworks has been in discussion with gummy processing OEMs about using the gummy technology but putting medical APIs in the formulation. In this case, the look and shape of the gummy would resemble traditional OSD (Oral Solid Dose) products so children don’t mistake the dose as a candy.

NW: Can the traditional method for forming/molding and packaging of gummies be improved?
Brower: Yes. There are a few interesting options to make the molding more efficient by cutting out process steps prior to blister packaging. Traditionally, the gummy is a hot-pour or dispensed into standalone molds. The molds are then accumulated, allowing time for gummy products to solidify. Molds are emptied and gathered as bulk to be packaged.
One concept to reduce the number of steps required is to dispense the product into molds that are indexed on an automated carousel. These indexed molds can be directly cooled while in motion. This automation can be in proximity if not directly coupled to a blister machine. Products can be picked from the indexed molds and fed directly into blisters. Pharmaworks has experience feeding these types of products directly into our family of blister machines. Blister rates can be scaled from 50 BPM on the TF1 blister machine to over 300 BPM on our TF3 blister machine.

An alternative method involves directly dispensing the formulation into blister cavities, thus eliminating several steps in the process. The challenge in this case is that the dispensed formulation is very warm—more than 100°C. Common thermoform materials like PVC, PETG, Aclar all require heating to nearly 110°C to form correctly. Obviously, the temperature of the product could deform these base materials/cavities. Intense cooling of the formed material prior to and during dispensing could mitigate this challenge but requires further testing. Alu/Alu base materials may be an option since the cavities are formed without heat and can retain integrity during the warm-fill process.
