By: Robert Green
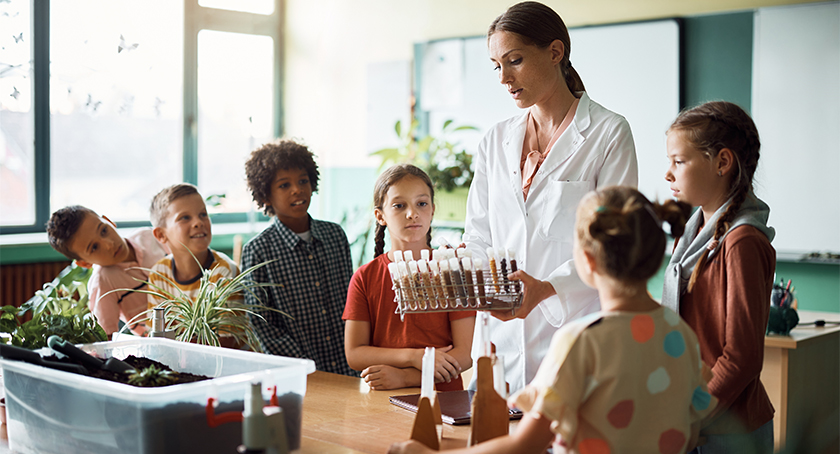
The Laboratory Notebook
Answering important questions about quality.
By Robert Green
Welcome to the second edition of The Laboratory Notebook. The response to our first column was tremendous, proving our belief that, despite what the pundits say, a large segment of our industry does indeed care about the quality of their products. Let’s review a sampling of the questions we received.
I see that most nutritional supplements are tested “by HPLC.” Who is HPLC and what makes him/her so smart?
HPLC is a method of analysis and not a person (but then you knew that). HPLC stands for “High Pressure Liquid Chromatography” (also known as “High Performance Liquid Chromatography”). Chromatography is simply a way to separate complex mixtures by passing them through a media that selectively absorbs materials. For a simple example, if we wanted to know how much chocolate is in a glass of chocolate milk we could pour the contents of the glass into a tube filled with material that would absorb (retain) the chocolate, allowing the milk to exit the tube. Next we add a solvent in which only chocolate is soluble. This then dissolves the absorbed chocolate and allows it to pass through the tube so we can then measure it for our answer. That’s the entire theory of chromatography. The “liquid” indicates that the material we are testing is in liquid form (a solvent is added to all samples before they are injected into the test equipment). The “high pressure” indicates that we are using liquids under pressure that increases the ability to separate complex mixtures. Today’s HPLC systems are computer-controlled using sophisticated software. They contain carousels that hold over 100 samples at a time and at the busy labs they run 24/7. The written record of the data generated is called a “chromatogram.”
While it sounds simple in theory, chromatography is actually much harder in practice. It is very hard to separate and then measure the minute quantities we must look for. For example, when we are analyzing ephedra we actually separate and then measure six closely related ephedra alkaloids. By reviewing the relationship between these six components we can tell many things, including if a synthetic component, such as ephedrine, was added to the herb to make it more “potent.” It is an enormous undertaking to perfect the best way to conduct an HPLC analysis and be sure the process works consistently over time. The most effective method is the correct combination of the solvent(s) that selectively solubilize the materials at hand (called the “mobile phase”), the media we use to temporarily absorb the material we want to identify (this media is housed in a column and is called the “stationary phase”) and the detector we use to measure the material we are looking for. To demonstrate the multitude of combinations, mobile phases come in various types, such as isocratic, gradient, polar and non-polar; stationary phases include normal phase, reverse phase, size exclusion and ion exchange; and detectors can be refractive index, near-infra red and ultra-violet (which can also be fixed wavelength, variable wavelength and diode array).
One of the critical conditions that we see routinely ignored by labs interested more in the volume of samples tested than the quality of analysis is the time the instrument is given to analyze the sample. Using our simple example, once the chocolate is passing through the tube for analysis it must be pumped at a slow enough rate so that the detector can see not only the chocolate but also the chocolate impurities that may exit the tube either immediately before or immediately after the pure chocolate. If the instrument speed is too fast both the pure and impure chocolate will exit the tube at the same time and the detector will be unable to distinguish them. This is one of the leading causes of disputes we see between analytical labs—one lab sets the instrument rate too fast so, with the pure and impure product lumped together, the sample looks primo. But in fact, at the proper speed, the impurities are revealed. Generally a run time of 20 minutes will work in most situations. A run time of four minutes (which we see all the time) is never sufficient. You cannot go too slow. You should ask your analytical lab for these details so you can determine if you are getting what you pay for. Or better yet, you should ask for a chromatogram that will report the duration of the sample run.
Now you know why you need to be sure the analytical lab you use not only has an HPLC but is fully qualified to use it and will take the time necessary to employ it correctly.
I purchased material from a supplier that insists it will only accept analyses conducted by its method. Should I worry?
Maybe. As we have said in the past, analytical chemistry is indeed a true science. There is only one correct answer when determining the specifications of a material (plus or minus a few percentage points, which we refer to as “experimental error”). Two experienced analytical chemists should be able to review an analytical protocol to determine if its use will result in an accurate analysis. In the case of your manufacturer, the proposed protocol should be reviewed by someone experienced in the field. It could be a perfectly reasonable method that can be used. Some manufacturers are fed up with inaccurate results obtained at labs that either lack the skill or dedication to conduct a proper analysis and specifying a responsible protocol up front can be an effective way to head-off a problem.
On the other hand, some manufacturers cheat (or at least stretch the truth). Recently we were asked to employ a manufacturer-supplied protocol that would have passed dirt (or close to it). In actuality, it was a colormetric test that, quite simply, calls for the addition of a dye and measurement of the resulting color. The trouble was this test was non-specific, so that other components in the sample reacted in the same way that the desired product did. The result was a test with outstanding results, which the manufacturer used to claim its product was the best available. In fact the product was mediocre at best.
My capsules with a target of 100 milligrams of L-Glutamine came out short. We took a 50 kilo drum of L-Glutamine with a purity of 96% and based our formulation calculations on 48 kilos of L-Glutamine in the drum (50 X 96%). What went wrong?
The problem probably relates to the common confusion between percentage purity and percentage assay. When we are asked for the percentage of purity of a sample and obtain a result of, say, 96%, that does not mean that 96% of the entire bulk material is the desired material. Simply stated, a purity analysis looks at the material that is the desired material (the pure stuff) or is close to the desired material (the impure stuff). However, it does not detect completely unrelated material, such as solvents, moisture or insoluble contaminants that require additional tests to measure. So in the L-Glutamine case the drum could contain a significant amount of moisture or an insoluble substance that is not detected in a purity determination. The differences between percentage purity and percentage assay can have dramatic effects on anyone purchasing raw materials (you may purchase material with a 98% purity but only 60% of the material you purchased is the desired material) and formulators (who may undershoot the contents of a capsule because the formula assumed 98% of the drum was the desired material when in fact it was not).
NW