Features
Supplement Safety Standards: Is Your Product Retail Ready?
Proof of product quality and GMP compliance are essential to access major retail platforms.
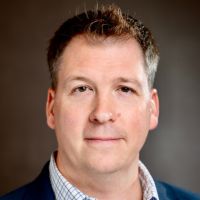
By: Sean Moloughney
Editor, Nutraceuticals World
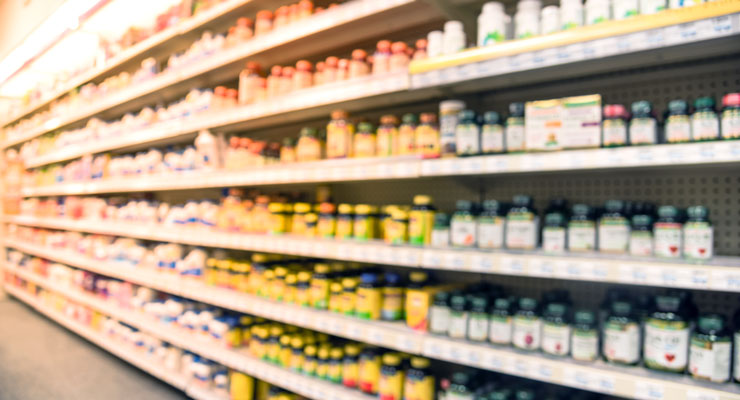
You don’t need a crystal ball to see what’s ahead for dietary supplement brands sold at major retailers. Several retailers and online platforms are already requiring supplement brands to show proof of Good Manufacturing Practice (GMP) compliance and independent ingredient testing before they will allow products to be sold on their shelves.
Amazon updated its dietary supplement seller requirements in April 2021 and CVS Health launched its Tested to be Trusted program in 2019. Both programs require brands and manufacturers to meet specific levels of quality assurance. Few in the industry will be surprised to see additional retailers and online platforms follow CVS’ and Amazon’s leads in the near future.
Opinions of these new retailer requirements are as wide and varied as the supplement industry itself. Some brands and manufacturers welcome the new requirements as a way to differentiate their products from competitors. Others see the new requirements as an unnecessary burden on brands and manufacturers. Nearly everyone is concerned about the potential for audit fatigue, scheduling nightmares, and added costs that might become the norm if individual retailers start creating their own unique quality and safety requirements.
We envision a future when most major retailers will require brands to show proof of product quality in some form or another, whether through independent assurance of GMP compliance, independent laboratory testing of products, or both. Supplement brands, manufacturers, and retailers are preparing for this changing landscape in different ways—and some are doing a better job than others.
New Retailer Requirements
What should brands do to prepare for the new retailer requirements? Taking steps to comply with Amazon’s new requirements may be a good start. After all, it’s not unreasonable to think other retailers will follow Amazon’s lead and adopt similar requirements. We’ve seen this happen in other consumer product categories, such as drinking water treatment devices and replacement filters. The online sales platform has tremendous influence over its brick-and-mortar competitors as well as other online retailers.
If you go this route, you won’t necessarily need to follow Amazon’s requirements word for word, but it’s a good idea to review the new retail requirements to understand the main elements of compliance. Most retailer product quality assurance programs include two main elements: assurance of Good Manufacturing Practices (GMPs) and finished product testing.
GMP Compliance. Brands and manufacturers must establish a process for periodic review of compliance with the requirements detailed in 21 CFR 111, the dietary supplement cGMPs. Ideally, this review should occur at least annually. While independent, third-party review of GMP compliance is not required by the U.S. FDA, many major retailers are now requiring third-party assurance of GMP compliance.
A regularly occurring, external review of your quality control system by an experienced and trusted partner is the best way to maintain compliance and avoid mishaps that can impact the quality and safety of your product. Frequent quality management system training is also required. If you decide to invest in an independent third-party audit of your GMP compliance, be sure to choose a partner that is accredited by ANAB to provide NSF/ANSI 455-2 dietary supplement GMP audit certification. We expect retailers to increasingly demand certification by an accredited certification body.
Finished Product Testing. Generally, major retailers are requiring, or considering requiring, a review of label claims and contaminant testing for every finished product. Contaminant testing ensures the product contains no undeclared ingredients or unacceptable levels of contaminants, while label claim review provides assurance that what’s on the label is what’s in the bottle or package. Testing and review by an independent, third-party ISO/IEC 17025 accredited lab is preferred, but some retailers do accept in-house laboratory testing under certain conditions. For example, Amazon accepts in-house finished product tests if you have first provided assurance of GMP compliance through an accredited GMP audit like NSF/ANSI 455-2.
Working with Contract Manufacturers
Maintaining compliance with retailer requirements takes some effort and advance planning, especially if you work with contract manufacturers. And most brands work with contract manufacturers at some point. In most cases, there isn’t a lot of vertical integration in the dietary supplements industry, except among the very biggest brands. Even these largest brands sometimes use contract manufacturers for specialty products like gummies, bars, and ready-to-drink (RTD) beverages.
If your brand works with contract manufacturers, you’ll want to take extra steps to help ensure and document compliance with GMPs. This starts with asking difficult questions. As the brand owner, you have a right to know what a contract manufacturer is doing to ensure compliance with GMPs. Don’t hesitate to ask. When working with a contract manufacturer, you’ll want to:
- Visit the manufacturing facility periodically to see production of your product.
- If you can’t physically visit the facility, ask your contact at the manufacturer to FaceTime or conduct a Zoom call with you during a walk-through of the facility.
- Review the manufacturer’s GMP certification or audit report. Any hesitancy in producing this documentation should be a red flag.
- Ask to see recent lab test reports for your products.
- Sign a quality agreement with your contract manufacturer.
The Quality Agreement
When working with a contract manufacturer, it’s essential to have a quality agreement in place. This can be a section in your formal business contract or an entirely separate agreement. The quality agreement details your expectations and addresses ownership of specific issues and responsibilities before any problem can arise.
It’s about accountability. What if a product is formulated too high? What if the product is contaminated with an inappropriate ingredient or allergen? If there is a problem, who owns it? If a recall is required, who will bear the cost? Who owns lab test results and the formulation? A quality agreement answers these questions and helps minimize finger pointing and heated arguments.
Unfortunately, many brands overlook this simple agreement when working with contract manufacturers. Established brands usually have rigorous quality agreements in place, but smaller brands often discover the need for quality agreements too late. For example, one U.S.-based supplement brand recently received a consumer complaint about the possible contamination of a product. When they asked to see recent lab test results, the contract manufacturer declined. It turned out the brand didn’t actually own the formula for its top-selling product. Discoveries like this—and disputes over quality—are all too common. Don’t wait for a crisis to determine who is responsible for your product’s quality.
Contract manufacturers also need to focus on new retailer quality requirements. In fact, contract manufacturers often find themselves making products for store brands as well as national brands. When making store-brand products, manufacturers will discover that retailers tend to dig in and take a close look at manufacturing practices. Retailers require their contract manufacturers to provide assurance of GMP compliance and product testing just as they would require it from a national brand. In this way, contract manufacturing organizations get a taste of what it’s like to be a national brand fighting for shelf space at a major retailer.
Leveraging Existing Standards
Almost every major retailer is discussing new quality requirements for supplements. Like CVS and Amazon, most retailers are looking for assurance of GMPs and finished product testing. Ideally, retailers will join together to harmonize their retail requirements—agreeing on a core set of requirements that are essential.
Organizations like the Global Retailer and Manufacturer Alliance (GRMA) have been working diligently to this end for several years. The alliance was formed in an effort to create and manage harmonized quality requirements in several non-food related industries, including dietary supplements, cosmetics, and over-the-counter drugs. Without harmonized requirements accepted by multiple retailers, brands have found themselves conducting duplicative and costly audits to document compliance with dozens of individual retailers.
Similarly, retailers can save themselves a lot of time and effort by either joining the GRMA, which uses the NSF/ANSI 455-2 dietary supplement GMP audit standard as its fundamental requirement, or by simply specifying compliance with the NSF/ANSI 455-2 dietary supplement GMP audit standard.
There’s no need to re-invent the wheel. NSF International already convened a balanced committee of supplement industry representatives, public health officials, regulators, and consumer interest groups to develop a consensus American National Standard for dietary supplement GMPs—NSF/ANSI 455-2.
Since NSF/ANSI standards are publicly available to anyone, it’s easy for retailers to use the NSF/ANSI 455-2 dietary supplement GMP audit standard as their own. Multiple certification bodies, including NSF International, are authorized to certify GRMA members to the NSF/ANSI 455-2 GMP standard. Alternately, manufacturers can choose to get independently certified to the NSF/ANSI 455-2 GMP standard by NSF International.
Retailers and Product Testing
Likewise, retailers don’t need to create their own product testing and label claim requirements. NSF International has already developed NSF/ANSI 173, the American National Standard for dietary supplements. This standard details requirements for finished products and includes rigorous criteria for:
- Label claims review;
- Toxicology review to certify product formulation;
- Contaminant review to ensure the product contains no undeclared ingredients or unacceptable levels of contaminants.
And since this is an American National Standard developed by a balanced committee of supplement industry representatives, public health officials, regulators, and consumer interest groups, it is available to anyone who wants to use it as the basis for their own product quality requirements. Certification to NSF/ANSI 173 is accepted by both CVS and Amazon as evidence of both GMP compliance and product testing. While NSF International is currently the only certifier accredited to certify products to this standard, any certification body can apply to ANAB to become an accredited certifier to the NSF/ANSI 173 standard.
I’m encouraged to see retailers and brands working together to establish retail requirements to protect consumers and differentiate quality products in the marketplace. This may be a paradigm shift for dietary supplement manufacturers, but it also presents a unique opportunity for brands to capitalize on new requirements. Global retailers are taking steps to increase consumer confidence and create a competitive advantage. Supplement brands can, and should, do the same.
About the Author: David Trosin is Managing Director of NSF International’s Health Sciences Certification group. In this role, he leads the ANSI-accredited certifier’s work with hundreds of dietary supplement manufacturers around the world. He played an instrumental role in the development of the NSF/ANSI 455-2 dietary supplement GMP standard. He has worked in the dietary supplements and functional foods sector for more than 25 years.